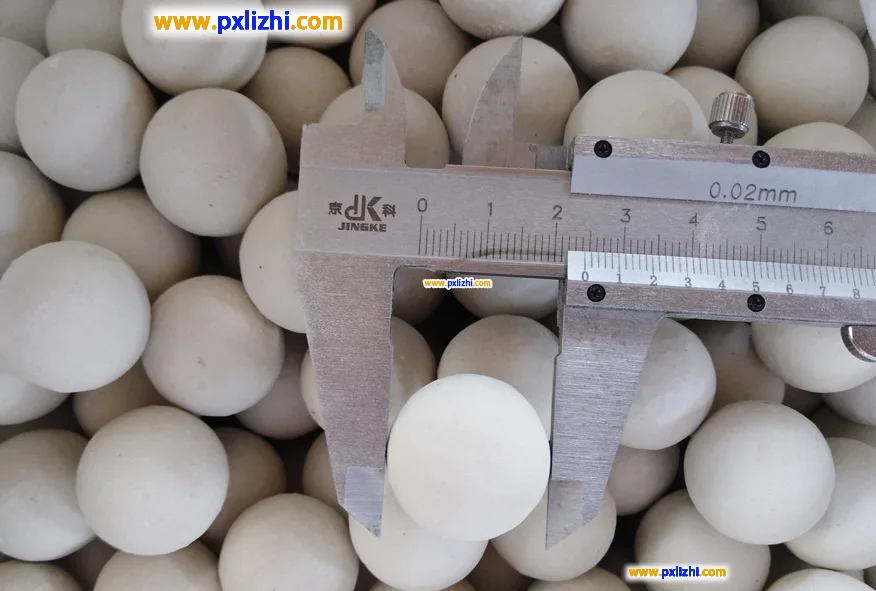
Firstly
the positive correlation between the alumina (Al₂O₃) content of inert ceramic balls and their quality and price is essentially determined by the material properties, performance advantages, and production process costs. The following analysis is conducted from both technical principles and economic logic perspectives:
I. Why does a high Al₂O₃ content enhance the quality of inert ceramic balls?
1. Material properties determine core performance advantages
Significantly enhanced high-temperature resistance
The melting point of Al₂O₃ is as high as 2050°C. The higher the content, the stronger the refractoriness and thermal stability of the ceramic balls. For instance, in chemical reaction furnaces or high-temperature flue gas treatment, ceramic balls with high Al₂O₃ content are less likely to soften, melt, or deform due to high temperatures, maintaining structural integrity for a long time.
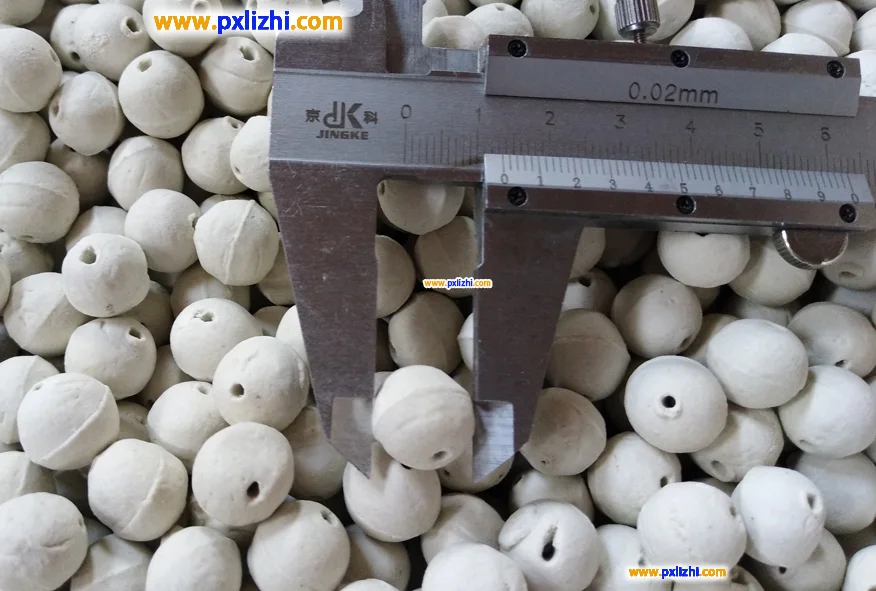
Superior chemical stability
Al₂O₃ exhibits extremely strong resistance to erosion in corrosive environments such as acids, bases, and salts. When the content exceeds 90%, the ceramic balls can withstand most chemical media except hydrofluoric acid (such as sulfuric acid, nitric acid, and strong alkali solutions), making them suitable for harsh chemical catalysis or filtration scenarios.
Improved mechanical strength and wear resistance
The Mohs hardness of Al₂O₃ is 9 (close to that of diamond). The higher the content, the more prominent the compressive strength (up to over 500 MPa) and wear resistance (wear rate < 0.1%) of the ceramic balls. For example, in fluidized bed reactors, ceramic balls with high Al₂O₃ content can reduce powdering caused by particle collisions and extend service life.
Optimized thermal conductivity and thermal shock resistance
The thermal conductivity of Al₂O₃ increases with the content (the thermal conductivity of pure Al₂O₃ is about 30 W/m·K), making the ceramic balls less prone to cracking due to thermal stress during rapid temperature changes, suitable for high-temperature to low-temperature cycling conditions (such as regenerative combustion systems).
2. Correlation between Microstructure and Properties
A high Al₂O₃ content promotes the formation of a denser crystal structure (with α-Al₂O₃ as the main phase) in the sintered ceramic balls, reducing the porosity to below 5%. In contrast, ceramic balls with a low Al₂O₃ content (such as Al₂O₃ < 60%) often have a higher amount of glassy or impurity phases, resulting in lower density, more defects, and a significant decline in performance.
II. Why does high Al₂O₃ content lead to higher prices?
1. Significant differences in raw material costs
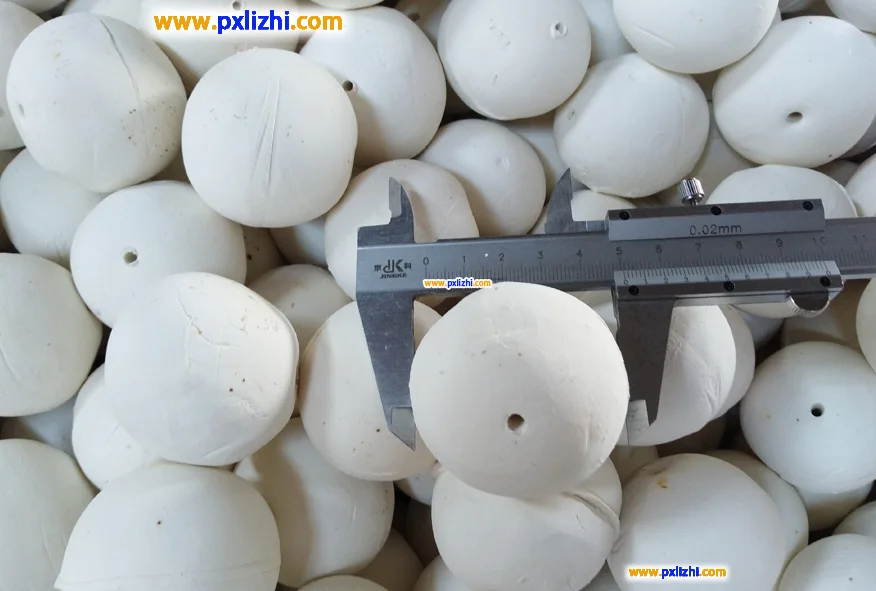
Scarcity of high-purity Al₂O₃ raw materials
The price of industrial-grade Al₂O₃ (with a content of over 90%) is 2 to 5 times that of ordinary industrial alumina (with a content of less than 70%). For instance, the price of high-purity Al₂O₃ powder with a purity of 99.5% can reach 50 to 100 yuan per kilogram, while the price of raw materials with a content of 60% is only 10 to 20 yuan per kilogram.
High cost of impurity control
To increase the Al₂O₃ content, it is necessary to strictly remove impurities such as SiO₂ and Fe₂O₃ (with a total impurity content of less than 0.5%). This can be achieved through mineral processing, chemical purification (such as the Bayer process), or sintering impurity removal processes. The cost increases exponentially with the increase in purity.
2. Complexity of production process and increased energy consumption
High-temperature sintering is difficult
High Al₂O₃ ceramic balls need to be sintered at 1600-1800℃ (low-content balls only require 1200-1400℃), which increases energy consumption costs by 30%-50%, and the maintenance costs of high-temperature sintering furnaces are also higher.
Costs of sintering aids and densification technologies
To promote the densification of high-purity Al₂O₃ sintering, trace amounts of sintering aids (such as Y₂O₃, MgO) need to be added or special processes such as isostatic pressing and microwave sintering need to be adopted, resulting in a significant increase in equipment investment and process costs.
Low yield and strict quality inspection
High Al₂O₃ ceramic balls are prone to cracking due to thermal stress during sintering, and the yield is usually 20%-30% lower than that of low-content balls. In addition, precise inspections such as X-ray diffraction (XRD) and scanning electron microscopy (SEM) are required to verify the crystal phase and structure, increasing the quality inspection costs.
3. High-end Application Scenarios and Market Positioning
High Al₂O₃ ceramic balls are mainly used in high-end fields such as petroleum refining (catalytic cracking units), semiconductor etching, and new energy battery materials. These scenarios have strict performance requirements, and customers are willing to pay a premium for high reliability, forming a “high cost – high pricing” market logic.
Ceramic balls with low Al₂O₃ content (such as 40%-60%) are mostly used in low-end fields such as water treatment and ordinary refractory materials. The market competition is fierce, and prices are sensitive, creating a price gap with high-end products.
III. Typical Application Scenarios and Corresponding Content
| Application Field | Recommended Al₂O₃ Content | Core Performance Requirements |
| Water treatment fillers | 40%-60% | Water resistance, low cost
| Chemical catalyst carriers | 70%-85% | Corrosion resistance, thermal stability
| Petroleum refining equipment | 90%-95% | High-temperature wear resistance, anti-coking property
| Semiconductor wafer cleaning | Over 99% | Ultra-low impurity leaching, high purity
The increase in the Al₂O₃ content in inert ceramic balls essentially aims to meet the demands of high-end applications by enhancing the intrinsic properties of the material, such as high-temperature resistance, corrosion resistance, and wear resistance. However, the use of high-purity raw materials, complex processes, and low yield rates have driven up production costs, ultimately establishing a positive correlation between performance, cost, and price. When making a selection, it is necessary to balance performance requirements and costs based on specific working conditions (temperature, medium, mechanical load), rather than blindly pursuing the highest content.