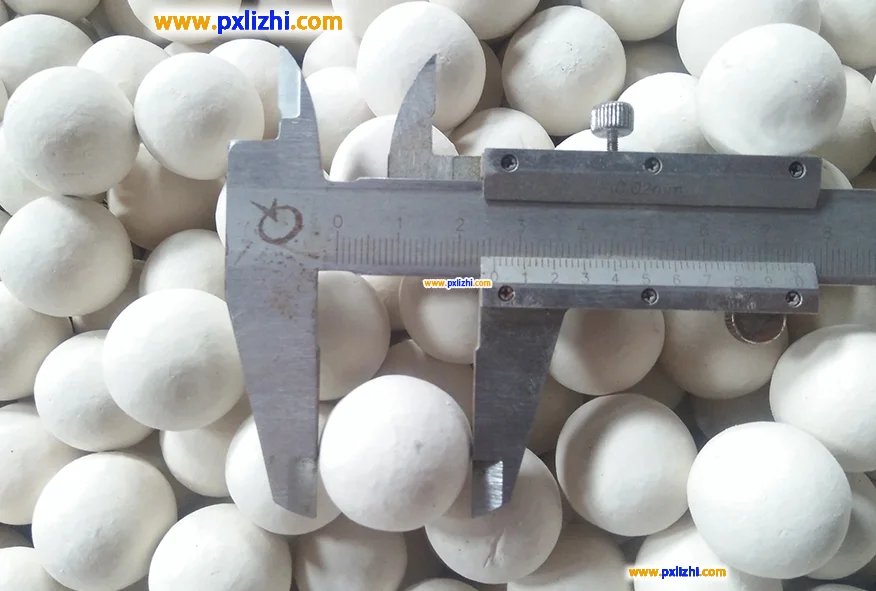
The strength of inert ceramic balls is one of its important performance indicators. If the strength is insufficient, it will cause a series of problems in practical applications. The specific impacts are as follows:
I. Direct Impact in Industrial Applications
1. Decreased mechanical properties, shortened service life
Increased risk of fragmentation: When subjected to pressure, impact or friction (such as as a catalyst carrier, or as packing material in a packed tower), weak ceramic balls are prone to break into fragments. For example, in chemical reactors, broken ceramic balls can clog pipelines or catalyst beds, resulting in reduced reaction efficiency.
Loss of structural stability: When used as a support layer (such as to support catalyst particles), broken ceramic balls can disrupt the uniformity of the bed, causing uneven fluid distribution and affecting process performance.
Increased wear: The surface of low-strength ceramic balls is more prone to wear, leading to smaller ball sizes and shape changes, which in turn affects their functions (such as the mass transfer efficiency of fillers).
2. Process efficiency is impaired
Mass transfer/heat transfer efficiency decreases: If used in a packed tower, the crushed ceramic balls will reduce the effective specific surface area, decrease the contact efficiency between gas and liquid phases, and result in poorer separation effects in distillation, absorption, etc.
Catalyst protection fails: As the support layer for the catalyst, the insufficiently strong ceramic balls cannot evenly distribute the fluid pressure, which may cause the catalyst particles to be compressed and crushed, affecting the stability of the catalytic reaction.
3. System failures and increased maintenance costs
Equipment blockage: Broken ceramic ball fragments flow with the fluid and may clog pumps, valves, or heat exchangers, causing downtime failures.
Frequent replacements and cleaning: Frequent replacement of ceramic balls is required, which increases labor costs and equipment downtime, especially in harsh conditions such as high temperature and high pressure, where the difficulty and cost of replacement are higher.
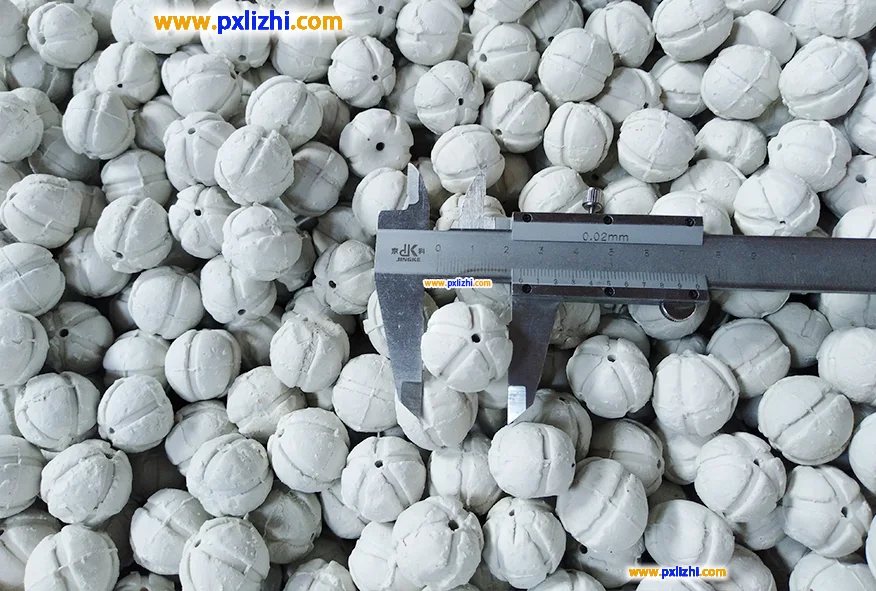
II. Specific Risks in Different Application Scenarios
1. Chemical and Petroleum Industry
Reactor/Tower Operation Issues: In catalytic cracking and hydrogenation refining units, the fragmentation of ceramic balls may lead to catalyst loss and even cause “channeling” (fluid bypassing parts of the bed) in the catalyst bed, resulting in (unqualified) reaction products.
Safety Hazards: The fragments may generate static electricity through friction, increasing the risk of fire in flammable and explosive environments.
2. Environmental field (such as waste gas/waste water treatment)
Filter efficiency decreases: When used as a filter medium, weak ceramic balls are prone to breakage, resulting in a wider particle size distribution of the filter material, and fine particles are discharged along with the water flow, affecting the quality of the effluent.
The deodorization/desulfurization effect of the packed tower weakens: Broken ceramic balls will reduce the porosity of the packing layer, decrease the contact time between the gas and the adsorbent/catalyst, and lower the pollutant removal rate.
III. Fundamental Causes of Insufficient Strength and Improvement Directions
1. Cause Analysis
Raw Materials and Formula Issues: Insufficient purity of the raw materials for ceramic balls (containing impurities), and improper proportions of sintering additives in the formula, can result in a loose crystal structure after sintering, leading to reduced strength.
Production Process Defects: Insufficient sintering temperature or insufficient holding time can cause pores in the ceramic balls; Inconsistent forming pressure leads to inconsistent density of the balls.
Usage Conditions Beyond Design Limits: For example, operating temperatures exceeding the refractory limit of the ceramic balls, or pressures exceeding the compressive strength threshold of the balls.
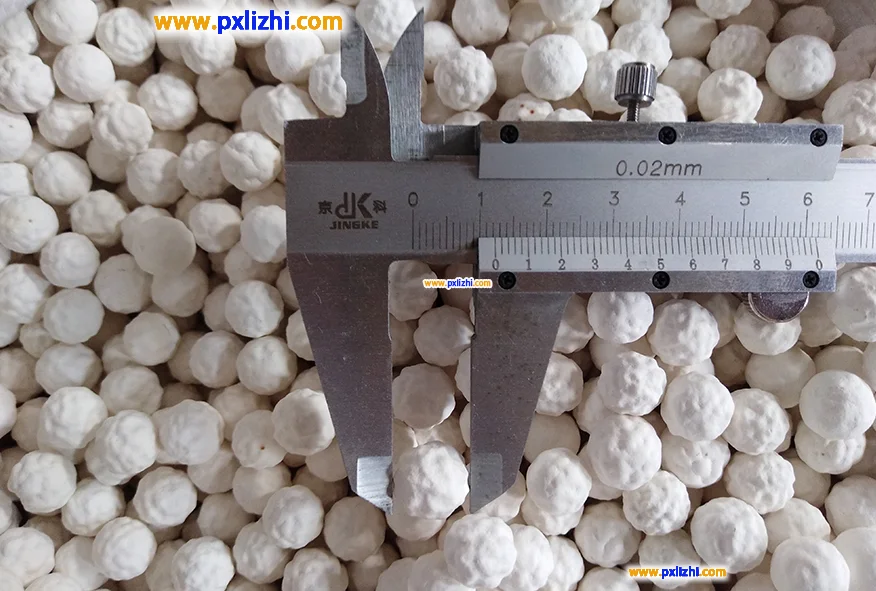
IV. Summary
The strength of inert ceramic balls directly affects their reliability and economic performance in industrial applications. Insufficient strength can lead to equipment failures, decreased process efficiency, and may also cause safety issues and environmental risks. Therefore, when selecting and using ceramic balls, it is necessary to strictly pay attention to their strength indicators (such as the compressive strength, which is usually required to be ≥ 5000N per ball), and choose products with appropriate materials and processes based on the working conditions to ensure the stable operation of the system.