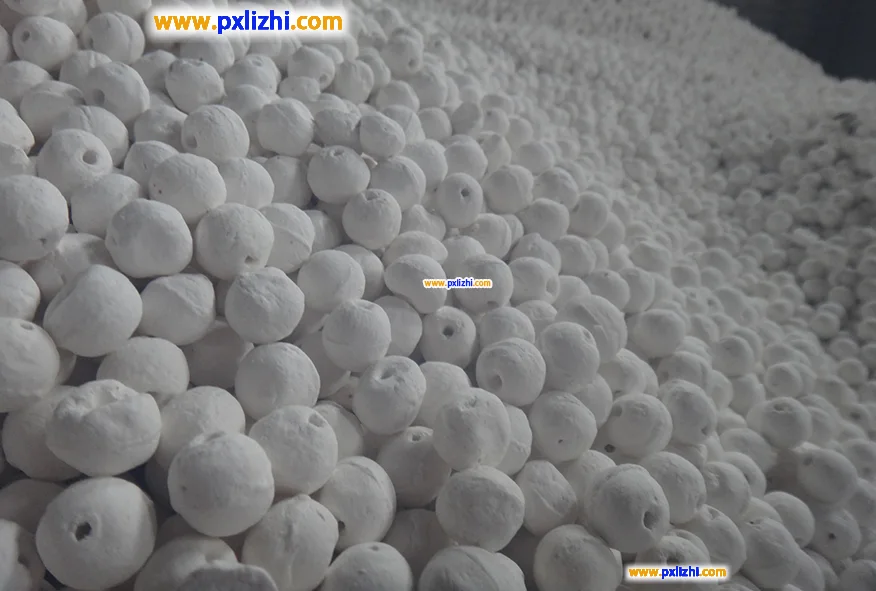
What are ceramic balls used for? Due to their excellent properties such as high hardness, wear resistance, high temperature resistance, and corrosion resistance, ceramic balls are widely used in various fields including industry, chemical engineering, and research. The following provides detailed explanations of their uses in different application scenarios:
1. Industrial and Chemical Environmental Protection
Catalyst Support and Distribution Layer: In fixed-bed reactors for petroleum refining (such as catalytic cracking, hydrogenation refining), chemical synthesis (methanol synthesis, ammonia synthesis), and natural gas processing, it is laid at the bottom or top of the catalyst layer.
Function: Uniform distribution of medium: To ensure that gases or liquids reactants pass uniformly through the catalyst layer, avoiding “channel flow” (where local flow velocity is too high, resulting in insufficient reaction).
Protecting the Catalyst: To prevent catalyst particles from directly contacting the bottom support structure of the reactor, avoiding crushing; at the same time, buffering the impact of gas flow, prolonging the catalyst’s lifespan.
Inert Isolation: Not reacting with high-temperature, highly corrosive reaction media (such as sulfur-containing, chlorine-containing gases), avoiding contaminating the catalyst or affecting the purity of the reaction products.
Typical Cases: In the reforming reactor of an oil refinery, inert alumina ceramic balls serve as the support layer, withstanding high temperatures (500-600°C) and oil gas erosion, while ensuring the stability of the catalyst bed.
Wastewater Treatment: In the biological filter of a wastewater treatment plant (such as an aerated biological filter BAF), inert ceramic balls serve as the filter material, filtering suspended solids in the water, and providing an attachment surface for microorganisms (although inert, the physical structure is suitable for biofilm formation).
Tower Packing and Distributors: In distillation towers and absorption towers, inert ceramic balls serve as bulk packing or distributor elements, promoting the contact between gas and liquid phases, and resisting medium corrosion (such as treating systems containing hydrochloric acid and sulfuric acid).
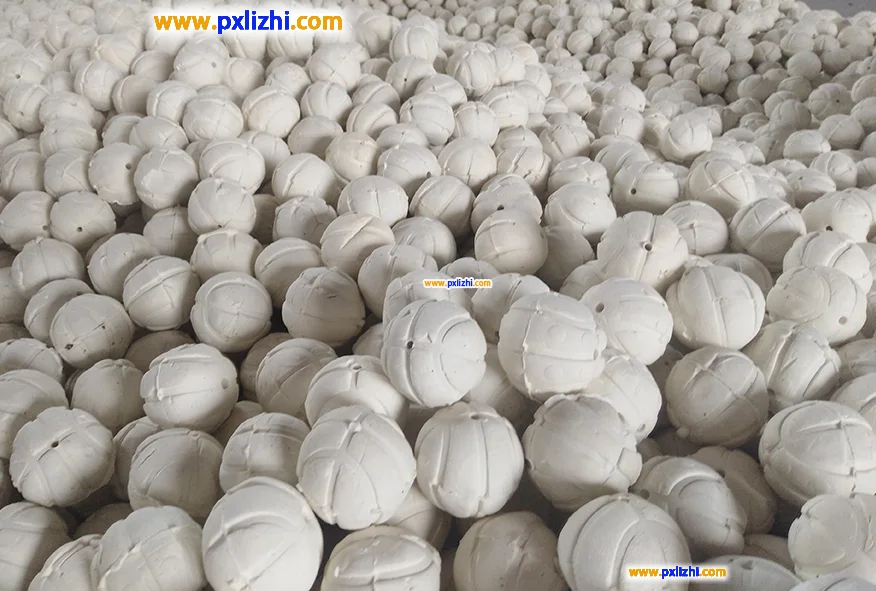
2. Grinding and Polishing Media
Application Scenarios: Used in equipment such as ceramic ball mills, sand mills, and agitated mills, for grinding minerals, pigments, electronic ceramic powders, lithium battery materials, etc.
Advantages: High hardness (such as ceramic balls made of aluminum oxide are close to diamond), high grinding efficiency with low wear on the media itself, and avoiding contamination of the materials (compared to metal grinding balls).
Typical Materials: 95% aluminum oxide ceramic balls, zirconia ceramic balls (with good toughness, suitable for brittle materials), silicon carbide ceramic balls (with good thermal conductivity, suitable for high-hardness materials).
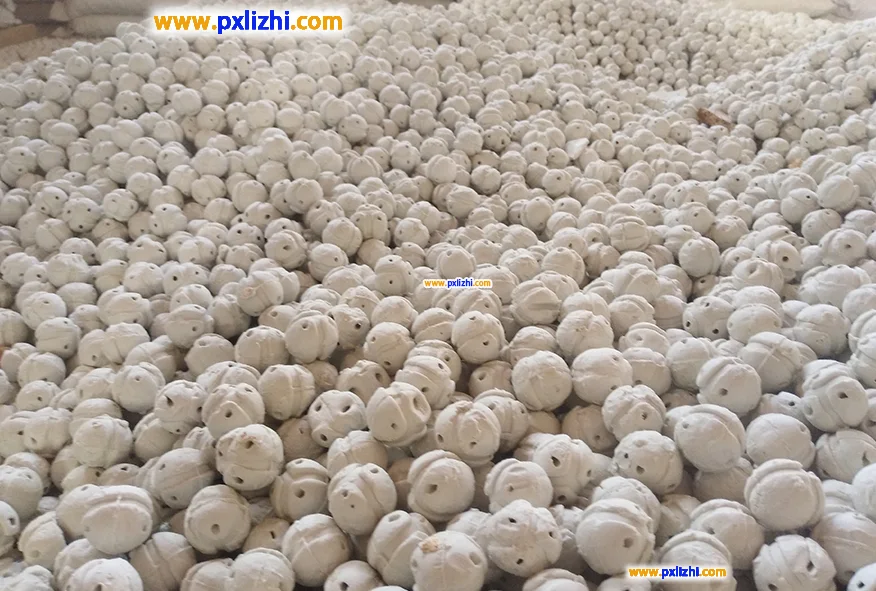
3. Bearings and Mechanical Components
Ceramic bearing balls: Used in high-speed motors, precision machine tools, aircraft engines, semiconductor equipment, etc., replacing traditional steel balls.
Advantages: Low density (light weight, reduces rotational inertia), high temperature resistance (such as silicon nitride balls can operate at 1200°C), corrosion resistance (not prone to rust, suitable for humid or corrosive environments), low friction coefficient (reduces energy consumption).
Mechanical sealing components: Used as sealing balls in chemical pumps and compressors, resisting corrosive media (such as acid and alkali solutions) and high temperatures, extending equipment lifespan.