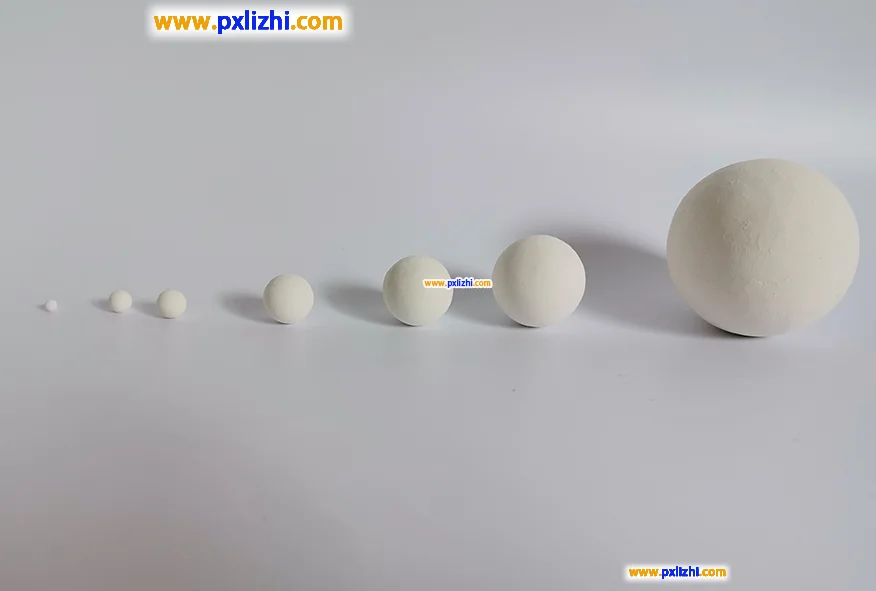
Various specifications of inert ceramic balls in terms of size and dimensions
I. What are inert ceramic balls?
Inert ceramic balls are spherical ceramic products made from raw materials such as alumina and kaolin through processes like batching, molding, and sintering. Their “inertness” is reflected in their extremely inactive chemical properties, hardly reacting with acids, bases, salts, and other substances, and being able to withstand high temperatures and harsh working conditions. Depending on the alumina content, they can be classified into common ceramic balls (aluminum content < 23%), medium alumina ceramic balls (30% – 70%), and high alumina ceramic balls (> 70% – 99%), among others.
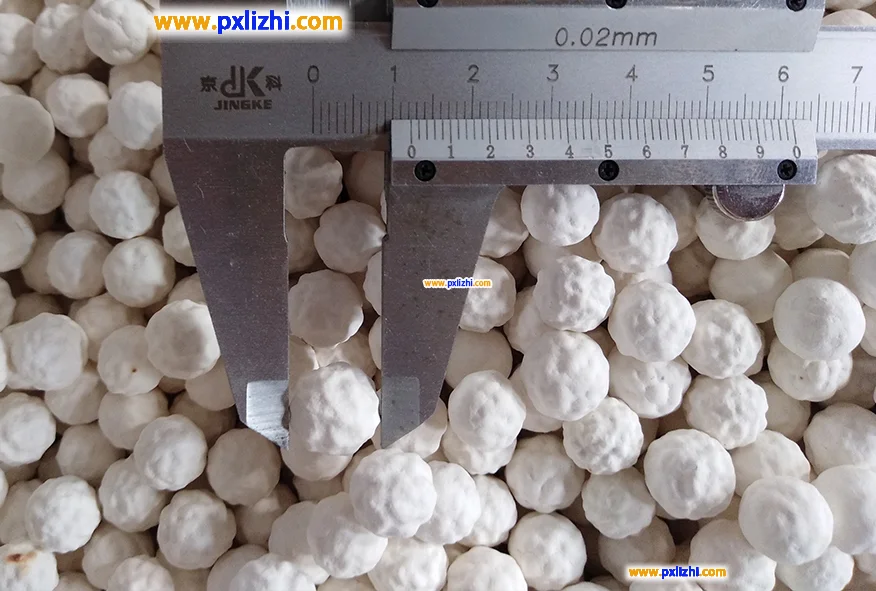
Concave-convex inert ceramic balls
II. What is its function?
1. Protecting the catalyst
In chemical reactors, inert ceramic balls are laid at the bottom or top of the catalyst layer to buffer the impact of high-speed gas flow or liquid on the catalyst, preventing the catalyst particles from being eroded, worn or crushed, and thus extending the catalyst’s service life.
For example, in petroleum hydrogenation reactions, it can prevent the catalyst from being deactivated due to impurities in the raw materials or pressure fluctuations.
2. Optimizing fluid distribution
Due to their smooth surface and uniform stacking, they can ensure that gas or liquid passes through the reactor uniformly, avoiding “channeling” and “deviation” phenomena, ensuring that the reaction medium fully contacts the catalyst and improving the reaction efficiency.
For instance, in desulfurization towers, they help the flue gas pass through the desulfurizer layer uniformly, enhancing the desulfurization effect.
3. High temperature and corrosion resistance
They can operate stably in high-temperature environments above 1000°C and resist the corrosion of strong acids (such as sulfuric acid, hydrochloric acid), strong bases (such as sodium hydroxide), and salt solutions, making them suitable for harsh chemical environments.
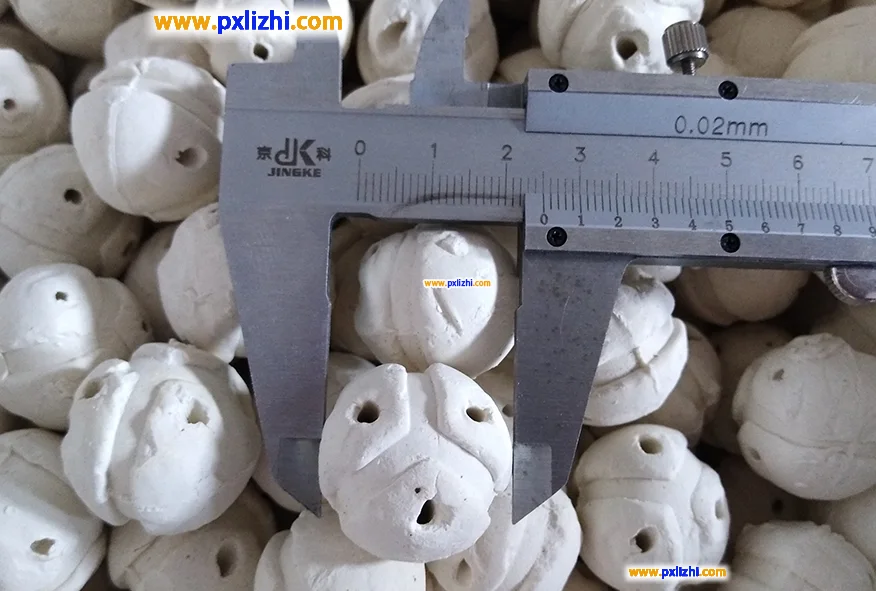
III. Where are the specific applications?
Petroleum and chemical industry: In catalytic cracking units and hydrogenation reactors, it serves as a catalyst support layer to protect the catalyst and evenly distribute the feedstock oil; in ethylene cracking furnaces, it buffers high-temperature gas flow and reduces catalyst loss.
Environmental engineering: In wastewater treatment, it is used as a filter medium to adsorb heavy metal ions or organic pollutants; in flue gas desulfurization towers, it supports desulfurization agents, optimizes flue gas flow, and enhances desulfurization efficiency.
Natural gas processing: In natural gas purification units, it supports desulfurization and decarbonization catalysts to remove H₂S, CO₂, and other impurities; it is laid at the bottom of storage tanks to prevent water accumulation and corrosion of the tank body, and to evenly distribute the gas.
Coal chemical industry: In coal-to-olefins and ammonia synthesis units, it supports catalysts in shift converters and methanol synthesis towers, stabilizing reaction conditions; in gas purification devices, it filters dust to protect subsequent equipment.
Other industrial fields: In ammonia synthesis towers and nitric acid absorption towers in fertilizer production; in packed towers and drying adsorbers in fine chemicals, it is used to support, distribute fluids, or protect core materials.
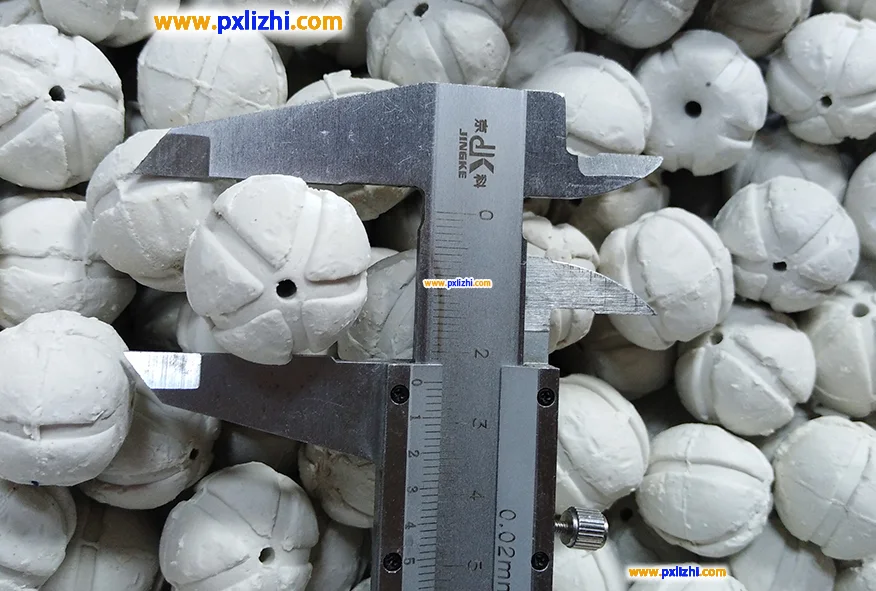
Summary
Inert ceramic balls, with their characteristics of corrosion resistance, high temperature resistance and high strength, have become key functional materials in fields such as chemical engineering, environmental protection and energy. Their core value lies in protecting core components, optimizing process efficiency and ensuring the long-term stable operation of industrial equipment.