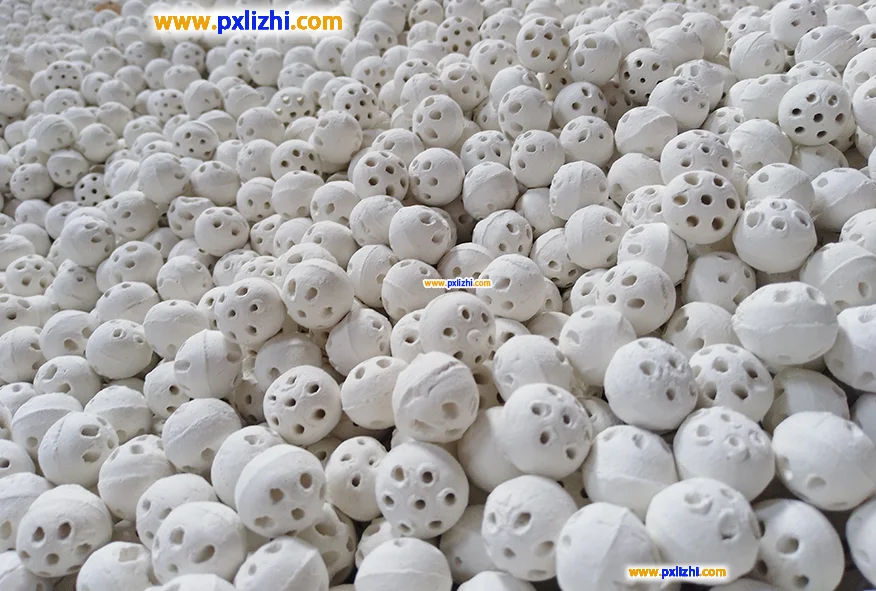
What is a ceramic ball made of?
A ceramic ball is a spherical object made of ceramic materials through specific processes. The different raw materials and manufacturing techniques used will result in different properties and applications for it. Here is a detailed introduction about the materials used to make ceramic balls and related content:
I. Main Raw Materials
The raw materials for ceramic balls are typically ceramic powders with high hardness, high temperature resistance, and corrosion resistance. Common types include:
Aluminum Oxide (Al₂O₃): One of the most commonly used ceramic materials, it can be classified into different grades based on the content of aluminum oxide (such as 95% and 99% aluminum oxide ceramics). It has high hardness (close to diamond), good wear resistance, and strong chemical stability, and is often used to manufacture industrial wear-resistant components, bearing balls, etc.
Zirconia (ZrO₂): It has good toughness and wear resistance, superior impact resistance to aluminum oxide, and a higher density (about 1.6 times that of aluminum oxide). It is often used to manufacture precision bearings, grinding media, or wear-resistant parts requiring high toughness.
Silicon Nitride (Si₃N₄): It has excellent high-temperature resistance (able to work at temperatures above 1200°C), anti-shock performance, and low friction coefficient. It is often used in bearings for high-temperature environments, mechanical seals, or high-performance components in aerospace and automotive industries.
Silicon Carbide (SiC): It has extremely high hardness (second only to diamond), good thermal conductivity, wear resistance, and corrosion resistance, and is often used to manufacture grinding balls, high-temperature bearings, or precision parts in the semiconductor industry.
Other materials
Such as talc ceramics, cordierite, etc., can also be used in specific scenarios (such as insulation, high-temperature insulation components), but their application range is relatively narrow.
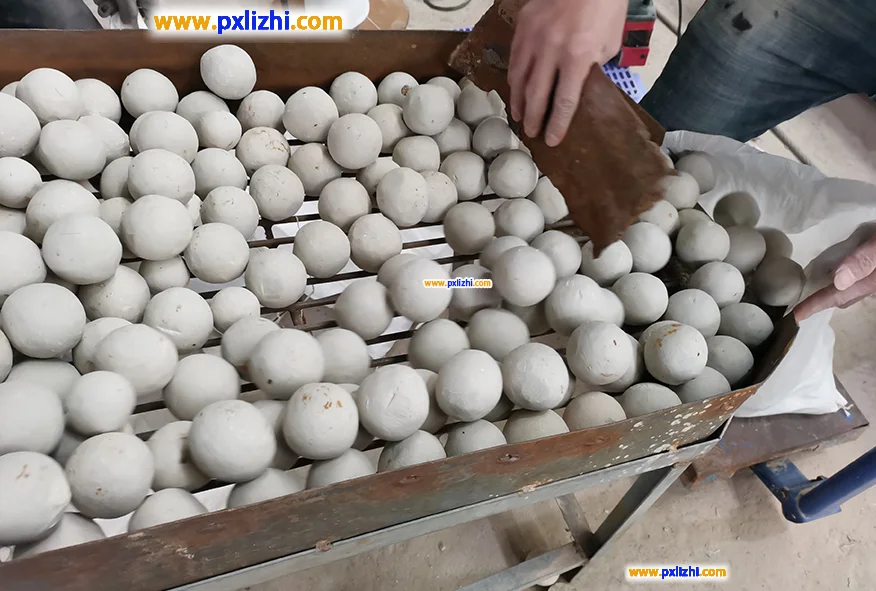
II. Manufacturing Process
The manufacturing process of ceramic balls typically involves the following key steps:
1. Powder Pre-treatment
The ceramic raw materials are crushed and ground into ultrafine powders (micron or nanometer level), and then sieved and impurities are removed to ensure the purity and uniformity of the powder particle size.
2. Forming
Dry pressing: The powder is placed in a mold and pressed into a spherical billet under high pressure (several to several hundred megapascals), suitable for mass production of medium-low precision ceramic balls.
Isostatic pressing: Utilizing the characteristic of uniform pressure transmission by a liquid, the powder billet is subjected to isotropic compression, resulting in a higher density and suitable for high-precision and high-strength ceramic balls.
Rolling: The powder is mixed with a binder, and then rolled into a ball in a roller, suitable for manufacturing ceramic balls of larger sizes (such as several millimeters to centimeter level).
3. Sintering
The formed billet is placed in a high-temperature furnace for sintering (the temperature is usually between 1300°C and 2200°C, adjusted according to the material).
4. Post-treatment
Grinding and Polishing: Multiple grinding processes (using diamond abrasive or ceramic grinding balls) are carried out to remove surface defects, improving the roundness and surface finish of the ball (with precision reaching micrometer or even sub-micrometer levels).
Cleaning and Inspection: Using ultrasonic cleaning to remove surface impurities, and through optical inspection, size measurement, and strength testing, qualified products are selected.
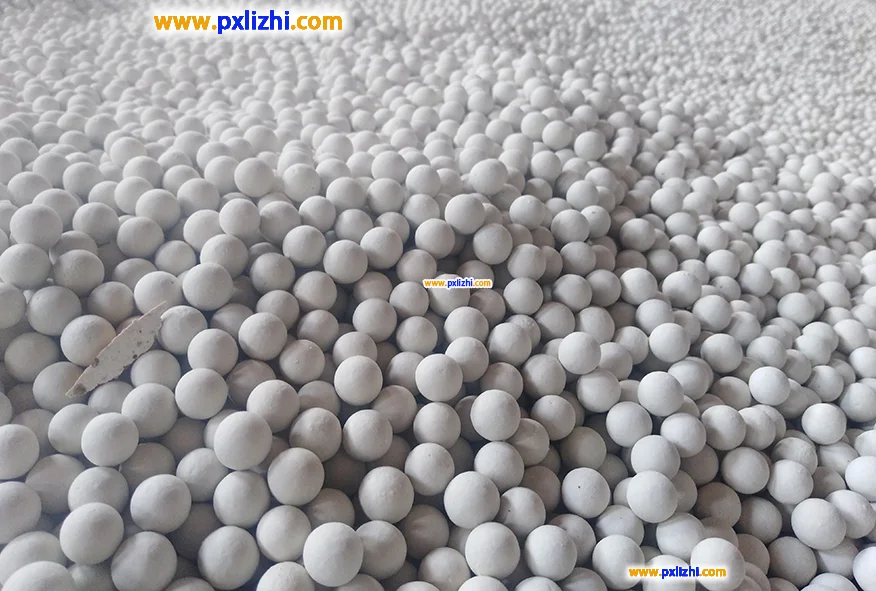
III. Performance and Applications
High hardness and wear resistance: Suitable for grinding media (such as grinding balls in ceramic ball mills), mechanical seals, and bearing balls (such as ceramic bearings).
High temperature resistance and chemical stability: Can be used in high-temperature furnaces, corrosion-resistant pipes, and aerospace engine components.
Insulation and low friction: As an insulating support in electronic devices, or to reduce frictional losses in precision instruments.
Biocompatibility: Some medical ceramic balls (such as zirconia) can be used in artificial joints and dental implants.
Summary
The core advantage of ceramic balls lies in their excellent physical and chemical properties, which are directly dependent on the selection of raw materials and precise manufacturing processes. From industrial wear-resistant components to high-end precision instruments, ceramic balls, with their “hard, durable, and stable” characteristics, play an irreplaceable role in multiple fields. If you need more specific application scenarios or process details, please feel free to provide additional explanations.