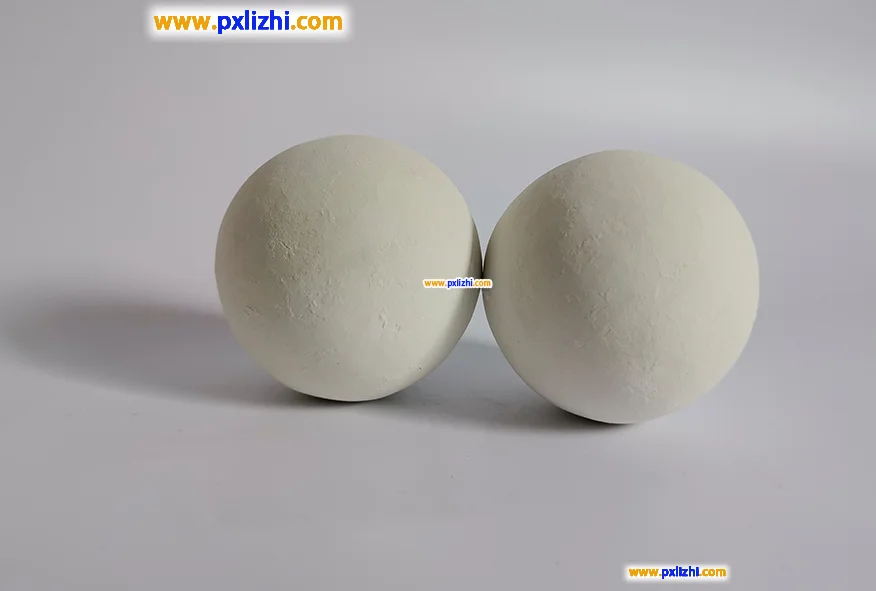
Preface
What is the purpose of ceramic balls?one must first know what types of ceramic balls there are? Different types of ceramic balls have different applications. Ceramic balls are mainly divided into two categories: inert filler ceramic balls for the chemical and petroleum industries and grinding ceramic balls for grinding purposes. The following is a detailed explanation.
The uses of ceramic grinding balls: Ceramic grinding balls are mainly used for efficient grinding and dispersion operations in fields such as minerals, chemical raw materials, and electronic materials. They can be used for coarse crushing and fine grinding of minerals like quartz sand and feldspar, achieving uniform particle size control in the grinding of lithium battery positive electrode materials. They are also suitable for the precise refinement of ceramic glazes and magnetic materials. Their high hardness and wear resistance make them suitable as dispersing media for liquid slurries such as coatings and inks, effectively breaking up pigment aggregates and improving the uniformity of the system. They can also be used as grinding media in ball mills and sand mills to achieve ultra-fine grinding of metal powders and glass powders, especially in the preparation of semiconductor wafer grinding fluids, where their low impurity release characteristics prevent material contamination and ensure the purity and performance of high-end products.
The uses of inert ceramic balls: Inert ceramic balls, due to their excellent chemical stability and corrosion resistance, are mainly used as packing materials in towers and vessels in fields such as chemical engineering, petroleum, and environmental protection. They can support catalysts and evenly distribute fluids in strong acid, strong alkali, or high-temperature conditions, such as in sulfuric acid production towers and natural gas desulfurization towers, resisting medium erosion. They can also be used as filter media in water treatment equipment to filter strong acid waste liquids or wastewater with high salt content without reacting with pollutants, maintaining pure water quality. They can also be used as inner lining materials in high-temperature kilns, maintaining inertness in firing environments above 1200°C to prevent chemical reactions with materials that affect product purity. They also have wear and heat insulation properties, extending the service life of equipment.
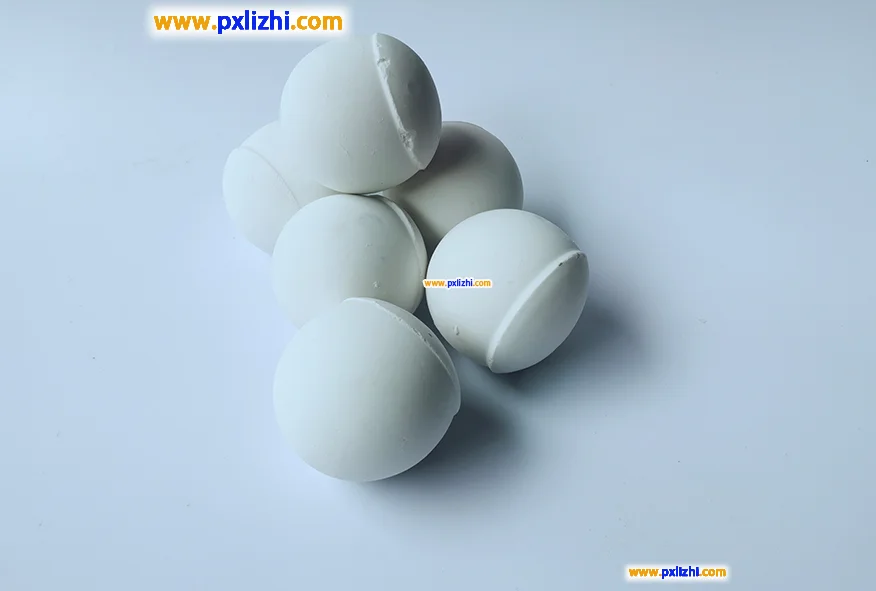
Classification of Ceramic Balls
- Classified by materials
Alumina ceramic balls: Made mainly of alumina, they can be classified into different grades based on the content of alumina, such as ordinary alumina ceramic balls (with lower aluminum content), medium-alumina ceramic balls (with aluminum content of 45%-70%), high-alumina ceramic balls (with aluminum content of 70%-90%), corundum ceramic balls (with aluminum content of over 90%), etc.
Silicon nitride ceramic balls: Made of silicon nitride, they have high strength, high hardness, high temperature resistance, low thermal expansion coefficient, good wear resistance and chemical stability. They are ideal materials for high-speed and high-precision bearings and are also used in aerospace, mechanical manufacturing and other fields.
Zirconia ceramic balls: Mainly composed of zirconia, they have good toughness, wear resistance, corrosion resistance and high-temperature resistance, and also have unique phase transformation toughening characteristics. When subjected to external force, they can absorb energy through phase transformation to prevent crack propagation, and are often used in precision instruments, electronics, medicine and other fields.
Silicon carbide ceramic balls: Made from silicon carbide, they have extremely high hardness, second only to diamond, and have excellent wear resistance, high-temperature resistance, thermal conductivity and chemical stability. They can be used to manufacture high-performance bearings, grinding media, bulletproof materials, etc., and have important applications in aerospace, energy, and mechanical fields. - Classification by Usage
Filler Ceramic Balls: Also known as inert alumina ceramic balls, they are mainly used in industries such as petroleum, chemical engineering, fertilizer, natural gas, and environmental protection, as a covering and supporting material for catalysts in reactors and as a packing material for towers. They can increase gas or liquid distribution points and provide support and protection for less strong active catalysts. They include ordinary ceramic balls, inert alumina ceramic balls, medium-alumina ceramic balls, high-alumina ceramic balls, concave-convex groove open-pore ceramic balls, active ceramic balls, open-pore ceramic balls, microporous ceramic balls, and heat storage ceramic balls, etc.
Grinding Ceramic Balls: They are used as grinding bodies in fine grinding equipment such as ball mills, cylindrical mills, and vibrating mills. They have the advantages of high hardness, large volume density, and corrosion resistance, and can improve grinding efficiency, reduce self-maintenance damage to materials, and are widely used in ceramics, glass, enamel, pigments, and chemical industries. Common types include silicon carbide grinding ceramic balls, microcrystalline medium-alumina grinding ceramic balls, and high-alumina grinding ceramic balls, etc.
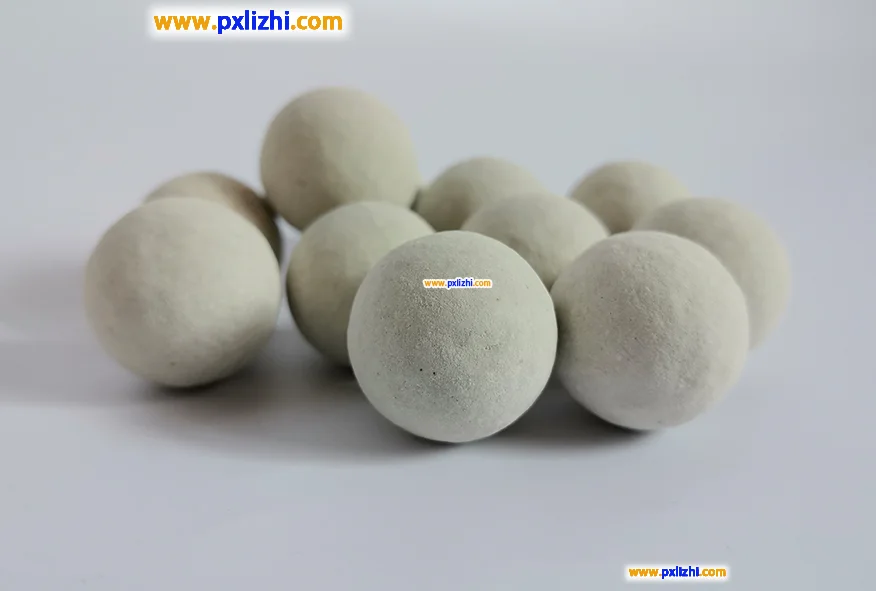
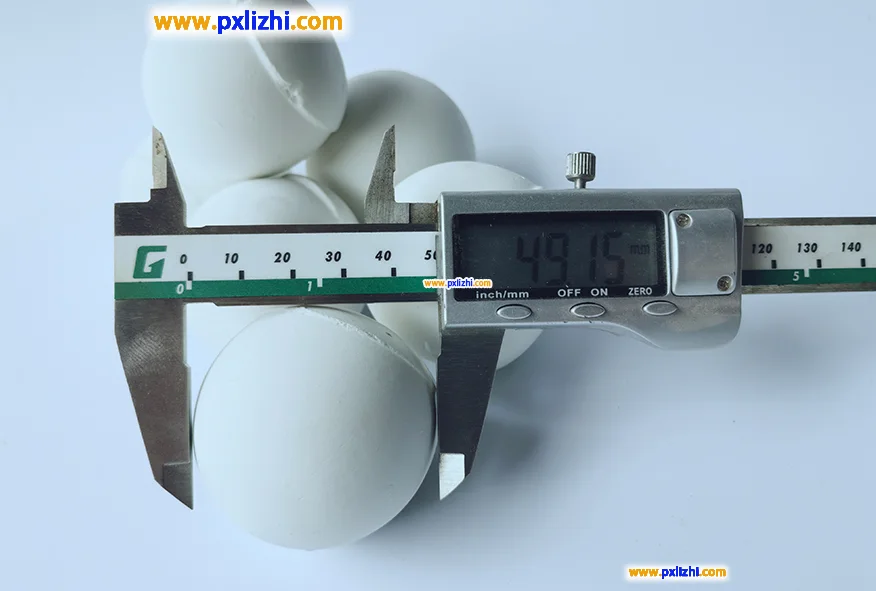
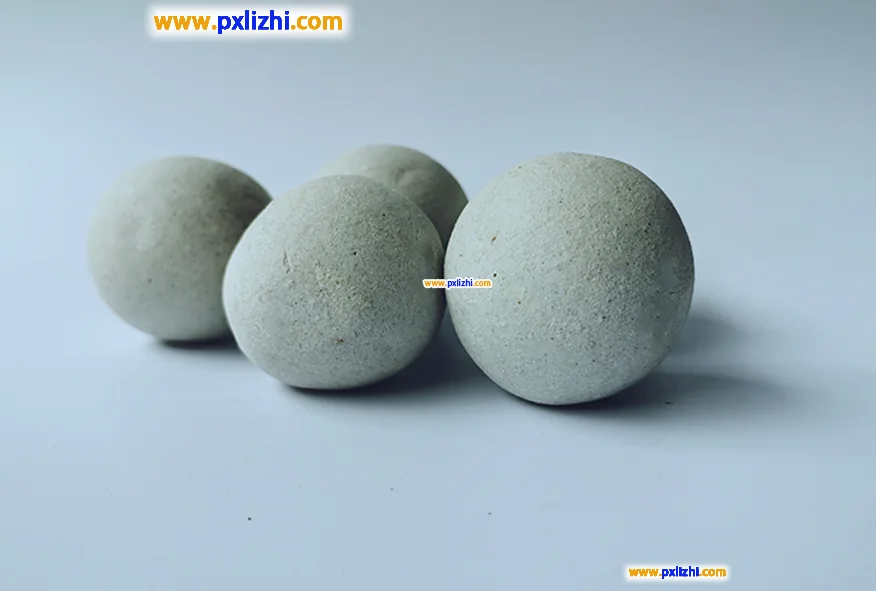